In asset management, Preventive Maintenance Strategies are a cornerstone for ensuring the longevity and optimal functionality of assets. A well-structured preventive maintenance strategy helps avert costly breakdowns and significantly enhances operational efficiency. This piece delves into the core aspects of preventative maintenance and outlines the detailed procedure to achieve a robust preventive maintenance program.
- Key Takeaways
- Definition and Importance of Preventive Maintenance
- Benefits of Preventive Maintenance
- Challenges of Preventive Maintenance
- Core Components of Preventive Maintenance Strategies
- Conducting a Review
- Standardizing Operating Procedures
- Creating a Reliability and Maintenance Policy
- Leveraging Technology
- Regular Monitoring and Evaluation
- Frequently Asked Questions
- Relevant Videos and Links
Key Takeaways
- Understanding and implementing preventive maintenance strategies is crucial for minimizing operational downtimes and extending asset lifespan.
- Standardizing operating procedures and leveraging modern technology are pivotal in advancing preventive maintenance programs.
- Regular monitoring and evaluation are essential for continuous improvement in maintenance practices.
Definition and Importance of Preventive Maintenance
Preventive maintenance is a proactive approach to maintaining assets in optimal working conditions, thereby minimizing the chances of unexpected breakdowns. Its implementation transcends routine checkups, delving into a systematic asset management strategy.
Benefits of Preventive Maintenance
- Cost Efficiency: Reduces the cost associated with reactive maintenance or unexpected breakdowns.
- Extended Asset Lifespan: Ensures assets remain functional over an extended period.
- Improved Operational Efficiency: Minimizes downtimes, thus enhancing productivity.
Challenges of Preventive Maintenance
- Resource Intensive: Requires significant time and resources for planning and implementation.
- Over Maintenance: The risk of overdoing maintenance activities may lead to resource wastage.
Preventive Maintenance Complete Guide provides an in-depth look into the importance and implementation of preventative maintenance strategies.
Core Components of Preventive Maintenance Strategies
A comprehensive preventive maintenance strategy encompasses three core components – Assets, Procedures, and People. Understanding the interplay among these elements is crucial for developing and implementing a successful preventive maintenance program.
Assets
- Identification: Cataloging all assets and understanding their current operational statuses.
- Condition Monitoring: Regular monitoring of asset conditions to preempt potential issues.
Procedures
- Standardization: Establishing standardized procedures for both reactive and preventive maintenance.
- Documentation: Documenting all maintenance activities for future references and evaluations.
People
- Training: Ensuring the maintenance team is well-trained and equipped to perform preventive maintenance tasks.
- Communication: Fostering a culture of open communication for reporting issues and sharing insights on maintenance practices.
This article, Five Strategies to Achieve World-Class Preventive Maintenance, elucidates how to harmonize these core components to develop a world-class preventive maintenance program.
Conducting a Review
Conducting a thorough review is the first step towards understanding the current maintenance practices and identifying areas of improvement.
Understanding Current Assets and Programs
- Asset Inventory: Having a precise inventory of all assets, conditions, and maintenance histories.
- Existing Maintenance Programs: Review existing maintenance programs to understand their effectiveness and areas of improvement.
Identifying Gaps and Areas for Improvement
- Gap Analysis: Identifying discrepancies between current maintenance practices and best practices.
- Recommendations: Develop recommendations for bridging identified gaps.
Standardizing Operating Procedures
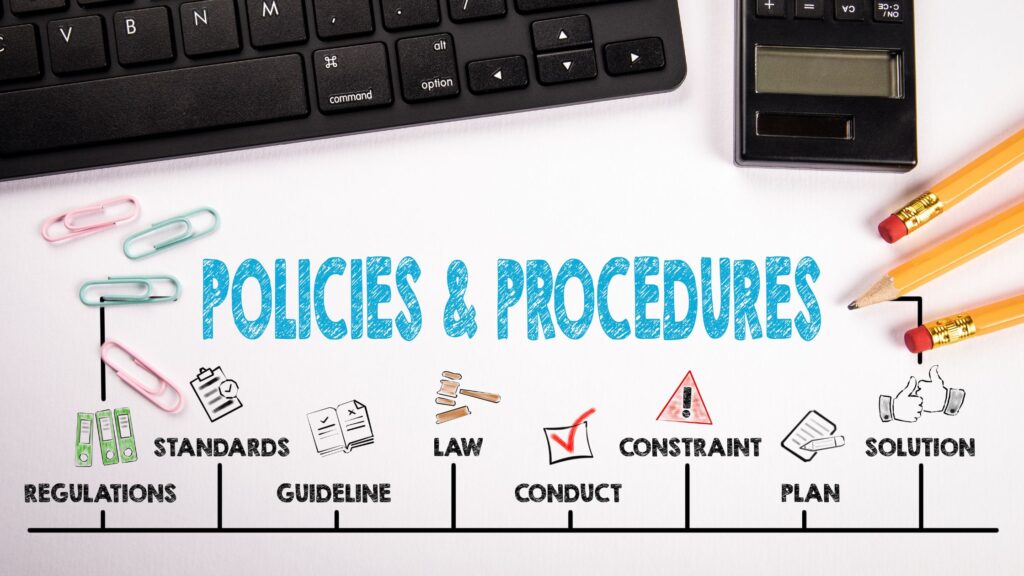
Establishing standardized operating procedures is fundamental for ensuring consistency in maintenance practices across the organization.
Importance of Standardized Procedures
- Consistency: Ensures maintenance tasks are performed consistently, regardless of who performs them.
- Quality Assurance: Helps in maintaining a high quality of maintenance work.
Case Study: Improving Maintenance Outcomes
A U.S.-based metal manufacturing organization experienced a significant reduction in downtimes by standardizing its operating procedures across all facilities. The case underscores the pivotal role of standardization in enhancing maintenance outcomes.
Creating a Reliability and Maintenance Policy
A sound reliability and maintenance policy lays the foundation for a cost-effective preventive maintenance program.
Establishing Objectives, Goals, and Key Responsibilities
- Objectives: Outlining the primary goals of the maintenance program.
- Goals: Setting measurable goals for evaluating the program’s success.
- Key Responsibilities: Defining the roles and responsibilities of each team member.
Incorporating an Improvement Plan with a Timeline
- Improvement Plan: Outlining a structured plan for continuous improvement in maintenance practices.
- Timeline: Setting a realistic timeline for achieving outlined objectives and goals.
Leveraging Technology
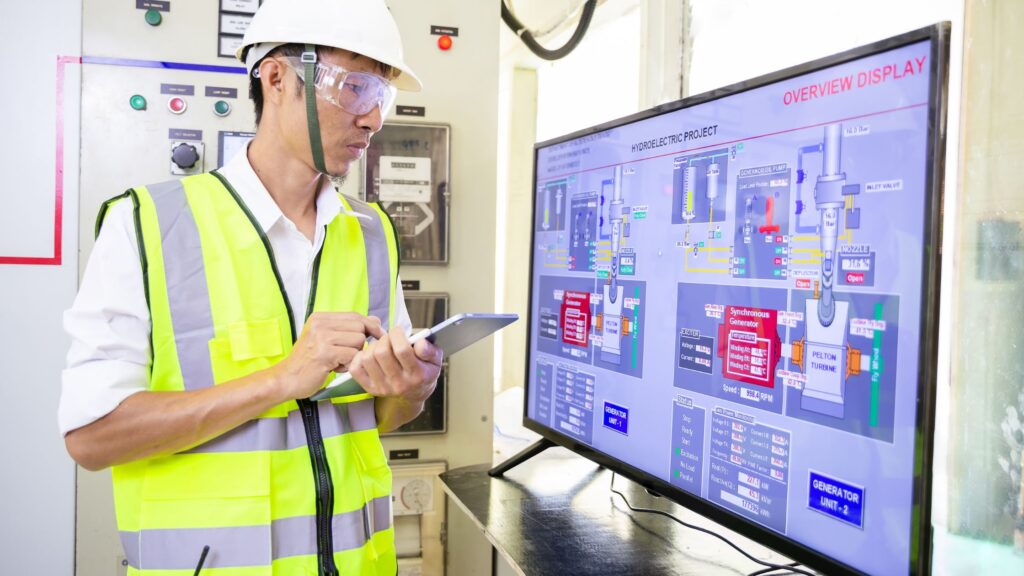
Technology is a linchpin in advancing preventive maintenance programs in the modern era.
Role of Computerized Maintenance Management Systems (CMMS)
- Automation: Automating routine maintenance tasks to save time and resources.
- Data Analysis: Utilizing data analytics to make informed maintenance decisions.
Case Study: Advancing Preventive Maintenance Programs
Leveraging a CMMS solution significantly reduced maintenance costs and improved operational efficiency in a manufacturing organization. The case highlights the transformative power of technology in preventive maintenance.
This marks the end of Part 1 of our exploration into Preventive Maintenance Strategies. The subsequent part will delve deeper into regular monitoring, evaluation, and other pivotal aspects of preventive maintenance.
Regular Monitoring and Evaluation
Regular monitoring and evaluation form the backbone of a successful preventive maintenance program. This section elucidates the pivotal role of continuous monitoring and the evaluation techniques contributing to preventative maintenance strategies’ overall effectiveness.
Continuous Improvement through Feedback
- Feedback Mechanism: Establishing a robust feedback mechanism for reporting issues and sharing insights on maintenance practices.
- Performance Metrics: Setting Key Performance Indicators (KPIs) for evaluating the program’s success and areas of improvement.
KPIs and Performance Metrics for Evaluation
- Operational Efficiency: Measuring the reduction in downtimes and improvement in operational efficiencies.
- Cost Efficiency: Evaluating the cost savings achieved through preventive maintenance practices.
Maintenance Audits
- Audit Procedures: Conducting regular maintenance audits to ensure compliance with established procedures and standards.
- Audit Findings: Utilizing audit findings for continuous improvement in maintenance practices.
Benchmarking
- Industry Benchmarks: Comparing the organization’s maintenance practices with industry benchmarks to identify areas of improvement.
- Benchmarking Analysis: Utilizing benchmarking analysis for setting realistic goals and achieving continuous improvement.
Technology in Monitoring and Evaluation
- Monitoring Tools: Leveraging modern monitoring tools for real-time tracking of asset conditions and maintenance activities.
- Data Analytics: Utilizing data analytics to evaluate the program’s success and identifying areas of improvement.
Frequently Asked Questions
- What are the core components of a preventive maintenance strategy?
- The core components include Assets, Procedures, and People. Understanding the interplay among these elements is crucial for developing and implementing a successful preventive maintenance program.
- How does technology contribute to preventative maintenance?
- Technology is pivotal in advancing preventive maintenance programs through automation, real-time monitoring, and data analytics, which aid in informed decision-making.
- What is the importance of regular monitoring and evaluation in preventative maintenance?
- Regular monitoring and evaluation are essential for ensuring compliance with established procedures, identifying areas of improvement, and achieving continuous improvement in maintenance practices.
Relevant Videos and Links
- Webinar on Preventive Maintenance Best Practices provides insights on supporting a robust preventive maintenance strategy in organizations.
- Top 5 Preventative Maintenance Strategies for Equipment discusses tasks to improve operating efficiencies and occupant comfort in equipment maintenance.
- A practical guide on How to Implement a Preventive Maintenance Program and Plan for asset-centric organizations seeking to avoid unscheduled equipment downtime.
Incorporating a robust preventive maintenance strategy is indispensable for any organization aiming to enhance operational efficiency and extend the lifespan of its assets. Organizations can significantly reduce maintenance costs, improve operational efficiency, and achieve long-term savings through regular monitoring, evaluation, and continuous improvement.
[…] Knowledge – Proficiency in building systems, construction, sustainability, maintenance processes, infrastructure life cycles and workplace technologies allows for informed planning and […]
[…] cleaning coils, checking the compressor, and ensuring the refrigerant levels are adequate. Regular professional inspections can identify potential issues before they become costly repairs. These tune-ups not only extend the […]